5 Tips To Manage The Warehouse
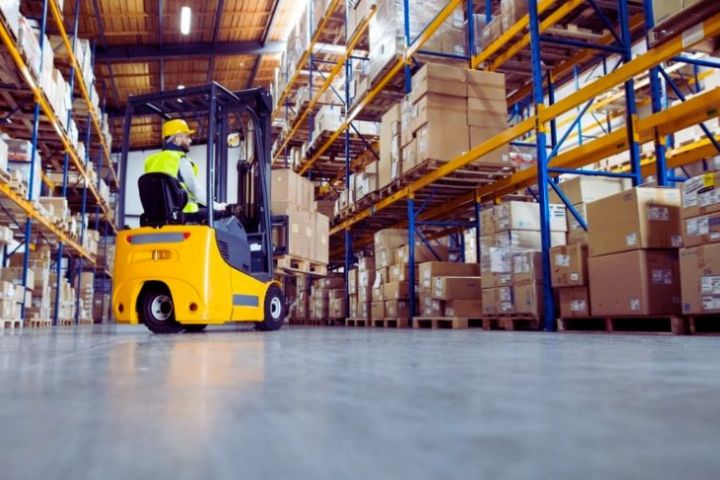
Tips To Manage The Warehouse : Maintaining optimal inventory levels is one of the main headaches for any company’s warehouse management. While it is true that it is thanks to our stocks that we can meet demand when it is produced by trying to fulfill our commitment to customer service, it is also true that inventory requires a capital investment that logically is not available for other uses that are also are of great interest. The problem is that investment in stock does not usually occur as a result of an express decision to dedicate more resources but as a consequence of multiple related factors, which means withdrawing financial resources to finance the warehouse without a conscious decision in that regard. This is why it is so important to manage the warehouse.
Let’s see how the most important factors act separately, which brings with it the lack of technology necessary to manage the warehouse and that will always result in excess inventory with a high risk of ending up becoming obsolete stock.
Among the most important factors to manage the warehouse, there are some that are closely related to the use of efficient technological tools. We can consider:
Table of Contents
1.- Shopping
The lack of knowledge of the real levels of current stock, of the optimal levels of stock to maintain or of the real consequences on the space, the costs, and the risks of saturation of the same, in addition to the fear of shortages and its consequences, frequently cause excessive acquisitions of raw materials and components, with which the department tries to protect itself from the responsibility of a stoppage due to shortages in the production line, for example. Other times, overstock appears due to excessive zeal when taking advantage of an offer or due to the inadvisable fact of letting ourselves be carried away by commercial or production pressure so that we maintain a constant and abundant stock of certain references.
If you are interested in further information on this SGA Success Case,
you can download a free ebook where you can delve into the achievements made.
2.- Work Deferred
What is the same, is work with information that is not updated at the time of use.
The flow of information must be totally reliable and must be transmitted in real-time, otherwise, the lack of immediacy can translate into an increase in the levels of our stocks.
The lack of exact and precise knowledge of our warehouse inevitably causes it to grow without any type of control or strategic or cost criteria since its growth only meets the criteria of “avoiding greater evils”.
3.- Big Differences Between The Input Flow And The Output Flow
If our finished product production batches are too large compared to the minimum sales batch and its frequency (if we manufacture 100 by 100 but sell 1 by 1 every 7 days) we will inevitably have increased stock levels and a high risk of obsolescence of all references where this circumstance occurs. Adjusting the flows in and out of a warehouse is essential to avoid this.
Reducing manufacturing batches as much as possible will allow us to gain flexibility, which will result in a better adaptation to changes in market trends, solve unforeseen events and possible incidents in less time and adapt our production capacity to the amount of real demand for our products. without the need to increase all our stock levels and maintain the level of customer service.
4.- Lack Of Demand Forecasting Tools
If we do not have support software to help us make reliable demand forecasts and we do not have a flexible and adaptable production system, we will accumulate stock to protect ourselves from market uncertainties.
The use of this software combined with the application of an MRP system (calculation of needs) adjusts deadlines and favors planning of production on more realistic sales forecasts. Production can adjust its deadlines and capacities without undermining the level of customer service or accumulating stocks.
5.- Lack Of Surveillance Of Warehouse Indicators
Managing a warehouse without an adequate WMS system reduces or completely eliminates control over certain management indicators that help us reduce inventory levels and prevent them from growing again. Indicators like ABCby rotation, the coverage rate, the average stock, maximum, minimum, and security stocks must be properly managed, paying greater attention, in terms of stock levels and counts, to products with high rotation over those with lower rotation.
The calculation of maximum, minimum, and security stocks alerts us to overstocks or possible breakages before they occur, giving us time to produce or buy what is needed and not do what we are supplied with. Comparing this data with the sales forecast, we will be able to have a coverage rate in time that will tell us how many days of stock we have for each reference, that is, at the current rate of consumption, how many days will I be able to supply the demand without producing more?
Conclusions
We have seen how the lack of technology causes unwanted consequences such as excessive purchases, lost opportunities, desynchronization between departments, the impossibility of planning, mismatches between inputs and outputs, loss of accuracy and immediacy in the information that results in lack of trust in the scarcity of a multitude of data and the lack of reliability of the existing ones. Consequently, or in response to all this, we inflate our stocks, either due to errors caused by inefficiencies in the system or due to excessive protective zeal.